工作機械の稼働率向上を図るためにグロサポを採用
事例紹介
Y社(従業員:約100名)
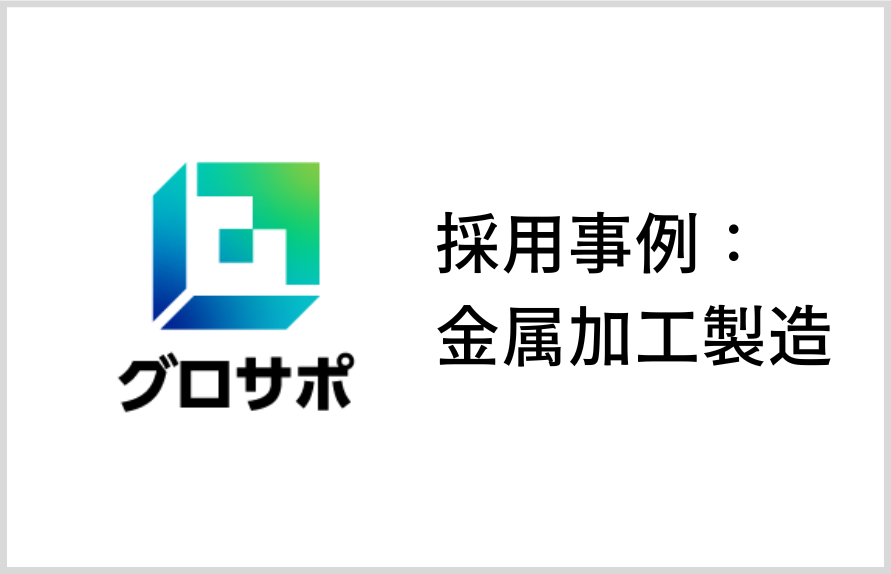
Y社では収益拡大、原価低減には、内製強化による外注費の削減が必要と考えていた。内製強化として、様々な改善活動に取り組んでいたが、海外への生産移管や熟練工の退職、多品種少量化も重なり、多忙の中、活動は下火となっていた。そんな中、共同検証を通じコンサルタント視点を交えた改善取り組みに手ごたえを感じてグロサポを採用頂いた。
課題整理
お客様の工場視察、責任者、関係者からのヒヤリングを行い、内製強化に向けて課題を整理した。
- 設備の稼働が低いとの肌感覚はあるが、稼働率を数値として把握できていない。
- 段取り時間やチョコ停などの停止時間、停止要因を記録しておらず、分析が出来ていない。
- 全体効率化視点での最適化ができていない。設備ごとに個別最適となっている。
- 改善成果が見えない。記録や報告ができていない。
課題解決へのアプローチ
役員を含めたトップ判断できる推進体制で、設備の稼働分析から詳細な稼働傾向の把握と対策について全社活動として着手した。
- 各設備の稼働率を把握する。設備の稼働状態は既存の積層信号灯からセンサーで自動的に情報収集する。
- 段取り変更やチョコ停などの設備停止要因は、手動入力のスイッチを利用し識別できるよう情報収集する。その他のロス時間は、手書きメモを活用し、リモートアドバイスの中で分析、改善につなげる。
- 可視化ツールにデータを投入して、工場全体の分析(総合設備稼働率)と各設備の稼働、停止時間とその内訳を数値で把握する。
- 課題進捗管理表を作成し、課題解決のプロセスを通してマネジメント力の向上やリーダー育成につなげる。
実現システム
実施結果(導入3か月)
- 段取り等の品種切り替え時間の短縮 19.1% → 5.5%(約4分の1に削減、約30時間/月の効果)
- 2時間以上の連続運転回数が増加することによる省人化4回 → 11回(約3倍に増加、約35時間/月の効果)
- 時間稼働率の改善 11.3% → 24.3%(約2倍に増加)
- リーダーの主体性、積極性がアップでき、改善活動記録が技術継承のノウハウ集となる。
※低価格にパッケージ化されたリモートアドバイスは、短時間ではあるが実績と経験に裏付けされた濃密な改善アドバイスと感じていただき、費用対効果を十分に理解いただいた。
今後
- 設備を増やし、工場全体の分析できる範囲を拡大する。効果の上がった改善成果を他設備に横展開する。
- 組織を横断した全社的な活動へと拡大し、全体効率化に向けて活動範囲を広げる。